Every day, countless workers enter confined spaces, where the margin for error is slim, and the consequences of oversight can be grave. This scenario is a breeding ground for anxiety, not just for the workers but for those responsible for their safety.
What if there was a way to not just react to confined space incidents but prevent them in the first place? This article explores the challenges of confined space work and introduces how physiological monitoring transforms how businesses approach confined space safety.
Understanding Confined Space Work
Many workplaces harbor areas known as confined spaces. These areas are not typically designed for human presence yet sizable enough for workers to enter and conduct specific tasks. They also have limited or restricted entry and exit points and are not intended for continuous occupancy. The variety of confined spaces is broad, encompassing tanks, vessels, silos, storage bins, hoppers, vaults, pits, maintenance holes, tunnels, equipment housings, ductwork, pipelines and more.
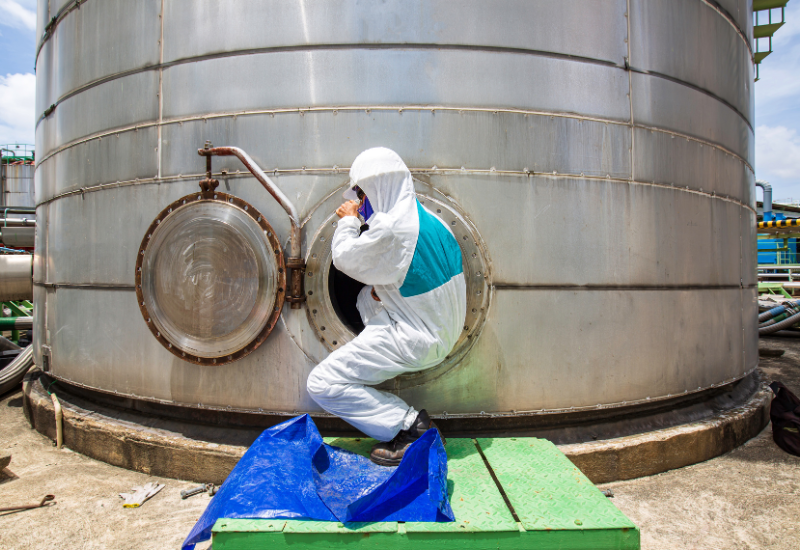
To address the unique hazards these areas present, OSHA defines permit-required confined spaces based on specific criteria. These spaces may contain or potentially contain hazardous atmospheres, materials that could engulf an individual, inwardly converging walls or downward-sloping floors leading to smaller areas that pose entrapment or asphyxiation risks. They may also contain other recognized safety or health hazards, including unguarded machinery, exposed live wires or conditions leading to heat stress.
Key Points:
- Limited Accessibility: Entry and exit points are often restricted, making it difficult for workers to quickly escape in case of an emergency.
- Not for Continuous Occupancy: These are not spaces where work happens regularly but are accessed for specific tasks like inspection, maintenance or repair.
- Potential Hazards: Due to their design and the nature of work performed, these spaces often contain or could contain hazardous conditions.
Industries at Risk
The scope of industries that engage in confined space work is extensive, underlining the importance of this work across various sectors. From construction workers accessing underground utilities to manufacturing employees performing maintenance inside large machinery, the necessity of entering confined spaces is a common denominator.
Other sectors heavily involved include agriculture (for silo entry), maritime (for ship repair) and even entertainment (for stage setup and take-down). These tasks are integral to the operations and maintenance within these industries, emphasizing the need for stringent safety protocols.
Key Industries:
- Construction: Accessing maintenance holes, sewers and underground utilities.
- Mining: Working in narrow veins and accessing underground chambers.
- Manufacturing: Maintenance tasks inside large machinery or equipment.
- Utilities: Inspection and repair of underground pipes and conduits.
- Agriculture, Maritime, and Entertainment: Specific tasks that require temporary entry into confined spaces.
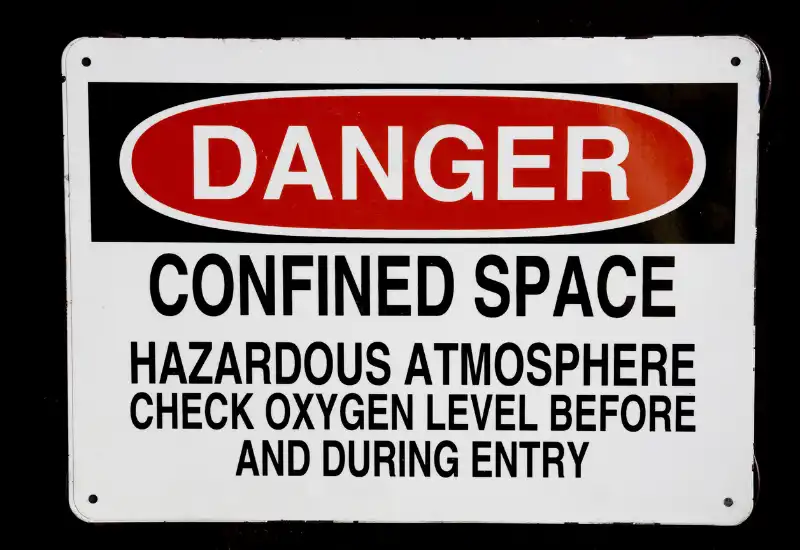
The Risks Involved
The multifaceted risks of confined spaces require workers and safety professionals to be ever-vigilant. Toxic gas exposure, for example, can occur with little warning, and without proper ventilation, the buildup of such gases can reach fatal levels quickly. The complexity of these environments means that risks are not always apparent, necessitating rigorous safety protocols and continuous monitoring to mitigate potential dangers.
Physical risks, such as slips, trips and falls, are compounded by the confined nature of these spaces, where maneuverability is limited. Psychological stress also plays a significant role, as claustrophobic conditions and potential isolation can impact mental health, emphasizing the need for comprehensive safety measures that address both physical and psychological well-being.
Key Risks:
- Atmospheric Hazards: Including toxic gas exposure and oxygen deficiency.
- Physical Hazards: These include the risk of fire, explosion and structural hazards leading to entrapment or collapse.
- Psychological Stress: The mental strain of working in confined, isolated conditions can not be overlooked.
To illustrate the risks of confined space, let’s say that a maintenance crew is assigned to perform critical repairs inside a large industrial storage tank, a known confined space with limited airflow and high potential for temperature variance. The team initiated the task during the peak of summer, underestimating the risk of heat accumulation within the confined area. Despite standard safety checks, the operation lacked specific measures for monitoring heat stress levels.
As the day progressed, the tank’s internal temperature rose significantly, exacerbated by the heat generated from the equipment and the lack of ventilation. Unaware of the escalating heat levels, the crew continued working until several members began showing symptoms of severe heat stress, including disorientation and exhaustion. The situation quickly necessitated an emergency response to evacuate and treat the affected workers.
This incident highlights the critical necessity for advanced monitoring solutions in confined spaces, especially those that can accurately measure and alert workers to dangerous heat conditions. Technologies capable of real-time monitoring of environmental factors such as eWBGT (Wet Bulb Globe Temperature), heat index, and humidity levels are vital. Such devices could have preempted the emergency by alerting the crew to the rising risk of heat stress, allowing for timely intervention.
Understanding confined spaces, the industries most at risk, and the inherent dangers is crucial for developing effective strategies to protect workers. It sets the stage for implementing advanced safety measures, including the use of technology like physiological monitoring, to not just respond to incidents but prevent them.
Traditional Safety Measures for Confined Spaces
Due to the inherent risks and challenges, confined space work requires stringent safety measures. Traditional safety protocols have served as the backbone of confined space operations, emphasizing the importance of manual checks, protective gear and established emergency procedures. These measures are critical for ensuring worker safety but also highlight the necessity for constant vigilance and adherence to safety standards.
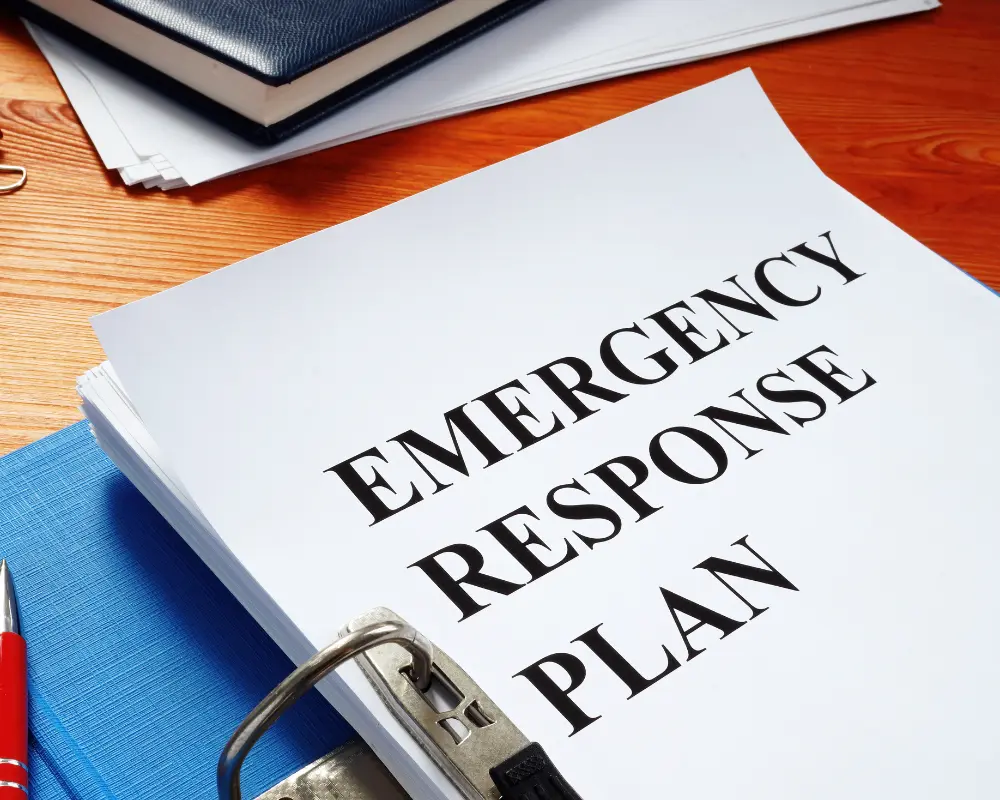
Key Components:
- Manual Checks: These include pre-entry inspections and continuous monitoring for hazardous conditions such as gas leaks or unstable structures.
- Protective Gear: Workers are equipped with PPE (Personal Protective Equipment) like helmets, gloves, respirators and safety harnesses tailored to the specific hazards of the confined space.
- Emergency Procedures: Detailed plans for evacuation, rescue operations and medical response in case of an accident.
The Limitations
While these traditional safety measures are indispensable, they come with inherent limitations, primarily their reactive nature. Designed to respond to emergencies, they often depend on the occurrence of a hazardous event to trigger a response. This approach, while necessary, underscores a critical gap in many traditional approaches to workplace safety—prevention.
Key Limitations:
- Dependence on Human Judgment: Many traditional safety measures require manual execution and interpretation, which can lead to errors or delays in response due to human factors such as fatigue or oversight.
- Reactive Nature: Traditional measures excel in mitigating the effects of an incident once it has occurred but are less effective in preventing incidents before they happen. For instance, PPE can protect a worker from the immediate impact of a fall, but it does not prevent the fall itself.
- Lack of Real-Time Data: Manual checks and monitoring provide snapshots of safety conditions but lack the continuous, real-time feedback necessary to anticipate and prevent potential hazards.
While necessary, reliance on these measures points to a critical need for more advanced safety solutions. These solutions should not only protect workers when an incident occurs but also offer the means to predict and prevent such incidents from happening in the first place.
The evolution of safety measures, particularly with the advent of technology-based solutions, aims to address these limitations by shifting from a reactive to a proactive safety model. This shift is crucial in enhancing the safety and well-being of workers in confined spaces where every second counts.
The Need for Advanced Safety Solutions
In today’s dynamic and often hazardous work environments, the complexity of tasks and the diversity of risks call for safety solutions that go beyond conventional methods. Integrating technology, especially physiological monitoring, represents a shift towards more sophisticated, proactive safety management practices.
The Technological Edge
Advanced safety solutions harness the power of technology to provide a real-time snapshot of environmental conditions and worker health. This real-time capability enables a shift from reactive safety measures, where actions are taken after an incident has occurred, to a proactive stance, preventing potential incidents through early detection and intervention.
- Customizable Alerts: Technology allows for customizing alert thresholds based on specific job roles, individual health profiles and environmental conditions, ensuring that warnings are relevant and timely.
- Integrated Systems: Combining data from wearable devices with environmental sensors offers a comprehensive view of the safety landscape, facilitating coordinated responses to emerging threats.
Real-time Health Data
The cornerstone of these advanced safety solutions is the ability to collect and analyze real-time health data from workers. This data includes not only basic metrics like heart rate and body temperature but also more sophisticated indicators such as hydration levels, exertion rates, and a variety of other biometrics.
- Predictive Insights: Beyond immediate alerts, analyzing health data over time can predict potential health risks before they become critical, allowing for preemptive health interventions.
- Personalized Safety Plans: Leveraging this data, safety managers can develop personalized safety and wellness plans that help address each worker’s specific needs and vulnerabilities.
The Importance of Monitoring
Monitoring physiological parameters is a critical component in the early detection of various health issues, particularly those aggravated in confined spaces, such as heat stress and exhaustion.
- Adaptive Work Environments: Real-time monitoring allows for the adaptation of work practices in response to the physiological state of workers, such as modifying work/rest cycles based on individual exhaustion levels.
- Environmental Adjustments: Besides monitoring workers, environmental monitoring can identify the need for adjustments in ventilation, cooling or heating to maintain optimal conditions for worker health and safety.
The integration of advanced safety solutions, particularly those focused on physiological monitoring, into the modern workplace, represents a significant advancement in the field of occupational health and safety. By leveraging real-time data, safety managers can not only respond more effectively to immediate threats but also anticipate and mitigate potential risks, ensuring a safer and healthier work environment for all.
SlateSafety’s Innovations in Safety Technology
SlateSafety is a leader in safety technology innovation. Their pioneering products, the BAND V2 and BEACON V2, are engineered with the modern workplace’s multifaceted challenges in mind. These devices display the potential of technology to revolutionize safety protocols, ensuring a safer work environment for all.
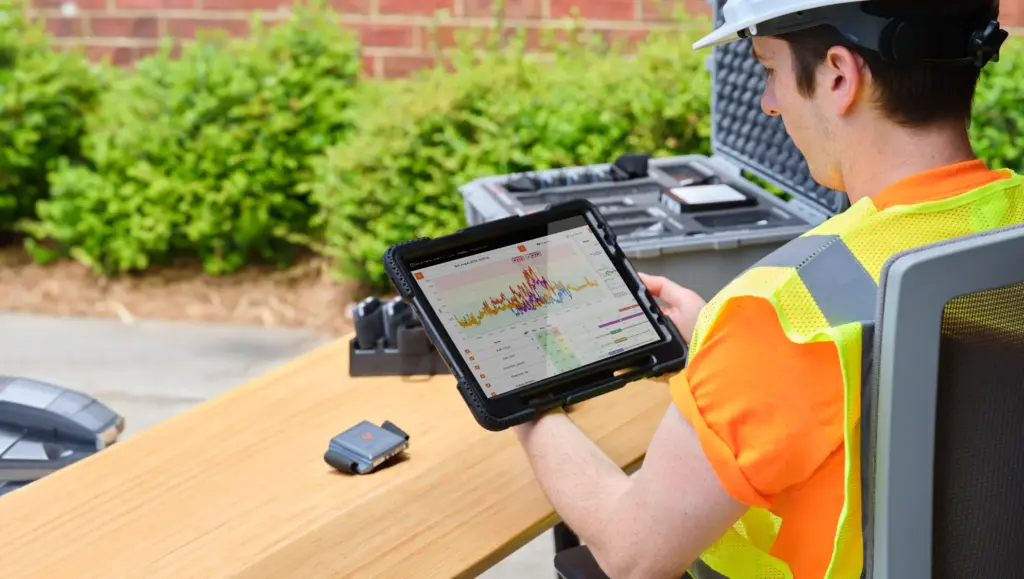
Real-time Monitoring
What truly sets SlateSafety apart is its commitment to real-time monitoring:
- BAND V2: This wearable device is a testament to SlateSafety’s dedication to worker health. By continuously monitoring biometric data such as Exertion, Core Body Temperature, Heart Rate, Heart Rate Limit Value (HRLV), Calories, Steps, Heart Rate Variability (HRV), and VO2 the BAND V2 can alert workers and safety managers to early signs of heat stress or physical overexertion. Its lightweight design and long battery life make it ideal for extended use in confined spaces and various work settings.
- BEACON V2: The BEACON V2 actively measures crucial environmental factors like eWBGT, Heat Index, Air Temperature, and Humidity, recognizing their significance in worker safety. This advanced device not only monitors confined space conditions but also acts as a Real-Time Locating System. With its innovative capability to detect sudden environmental changes, the BEACON V2 plays a key role in preventing incidents related to extreme heat.
A Comprehensive Safety Solution
The synergy between the BAND V2 and BEACON V2 offers a comprehensive solution that covers both individual worker health and the broader environmental context in which they operate.
- Data-Driven Decisions: Combining personal health data with environmental metrics enables safety managers to make informed decisions about work practices, potentially modifying schedules or tasks based on real-time conditions.
- Enhanced Communication: Both devices facilitate immediate communication between workers and safety personnel, promptly addressing any distress signals. This feature is particularly beneficial in confined or remote work areas where immediate verbal communication may not be possible.
- Worker Empowerment: SlateSafety’s technology empowers workers to take an active role in their safety by providing direct feedback on their physiological state and the surrounding environment. This empowerment is crucial for fostering a workplace culture of safety and accountability.
SlateSafety’s BAND V2 and BEACON V2 represent more than technological advancements; they signify a holistic approach to workplace safety. Through continuous innovation and a deep understanding of the challenges faced by modern workplaces, SlateSafety is setting new standards for safety technology.
SlateSafety: Embracing Technology for a Safer Future
Safety in confined spaces is a complex challenge, but the right technology can effectively address it. SlateSafety’s BAND V2 and BEACON V2 represent a significant step forward, offering a proactive approach to safety management. By adopting advanced safety technologies like physiological monitoring, we can transform confined space work from a high-risk activity into a well-managed operation.
For safety professionals and operations managers, the message is clear: embracing technological innovation is critical to enhancing worker safety in confined spaces. Explore SlateSafety’s solutions today and take the first step towards a safer tomorrow.